Kassim Textile
BROAD AC: Case Study of Feroze 1888 Mills
Feroze 1888 is a partnership between Feroze Group and 1888 Mills USA. It is one of the leading Manufacturer and Exporter of specialized Yarn & Terry products not only in Pakistan but across the globe. It is recognized as a Progressive and Global manufacturer of quality textiles for Home, Hospitality & Healthcare.
Feroze 1888 is a yarn and terry productscmanufacturing organization. The processes involved (which require HVAC) are open end spinning and weaving.
When the weft yarn meets the warp a fabric is created. The weaving is made on highly technological weaving looms through a complex process carried out with the utmost care, in a controlled environment, and with great experience of the weaving staff. For terry, there is a special pinching process which ensures the making of small thread ends which act as absorbents in towels etc.
Both Open-end Spinning and Weaving process require a controlled environment for better functioning of machines and superior end product quality. Ambient temperatures are controlled to remove the heat from machines and plant room, while humidity is controlled for superior end product quality. Usual requirement for open-end spinning process is humidity less than 50 and temperatures around 24-26 degrees Celsius. Usual requirement for weaving process is very high humidity levels and temperatures around 26 degrees Celsius. To meet the aforementioned environment requirements, Chillers and AC Plants are incorporated in the system.
In Feroze 1888, due to expansion of production, there was a requirement of chiller. They had installed two MTU engines and wanted to utilize the engines’ waste heat to produce cooling.
As the cooling requirement was high and the client had no other uses for exhaust gases, therefore BROAD proposed a very unique solution; Duplex Exhaust Chiller. BROAD Duplex Exhaust Chiller utilizes flue gases from two engines without risking the mixing problem and the back pressure issue through separate exhaust compartments for both engines. This fulfills client’s cooling requirement, reduces capital cost of project and conserves waste heat. BROAD also supplied the Packaged Water Distribution System. This system comprises of Chilled Water pumps (Soft Starter) and Cooling Water pumps (VFD), Filters, Check Valves, MCC, Water Softener, Biocide remover; all mounted on a skid. This system provides high savings through reduced electricity consumption and also reduces the installation time and space.
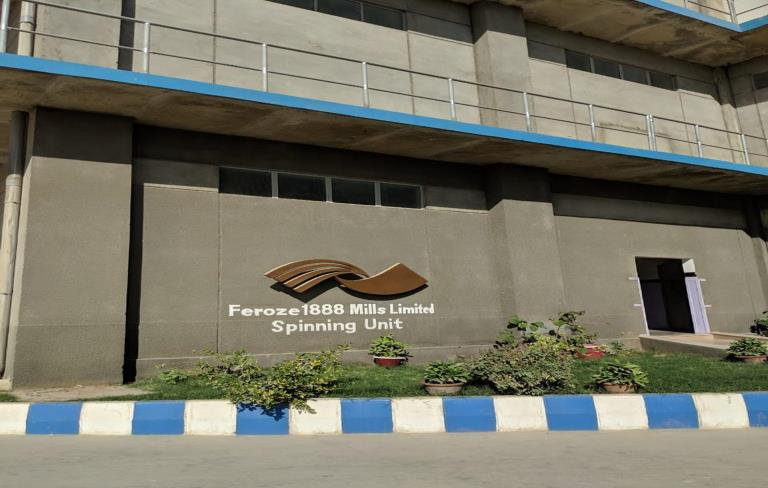
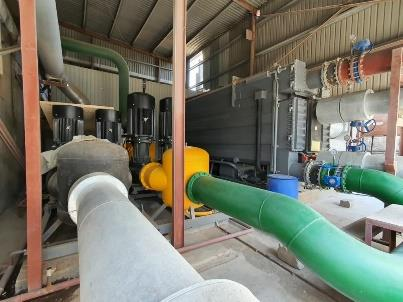
1) Total capacity = 830 USRT
2)Chiller with TITANIUM TUBES. Increased lifespan of 60 years.
3) High Quality Imported Factory Mounted Heat and Cold Insulation.
4) Efficient Plate Type Heat Exchangers.
5) Auto Purging and Venting System. Does not use vacuum pump for purging. Saves additives.
6) Compartmentalized structure (Separate inlet and outlet) reduces risk of back pressure and mixing. Reduces capital cost of equipment.
7) Smart Chiller. Able to control auxiliaries (Packaged Water Distribution System included) as per demand.
8) Real time online COP displayed on the chiller screen. Instant, Hourly and Daily COP indication.
9) Maximum number of parameters on screen.
10) Chiller is being monitored at BROAD Global Monitoring Center for free throughout chiller life span. Three tier monitoring Total.
11) Free of cost solution sampling service throughout chiller lifespan.
12) Efficiency of power house increased above 65% through BROAD chiller.
13) With waste heat recovery chiller, BROAD makes huge annual savings when compared with electric chillers. (PKR 30 Million approx.)
14) Packaged Water Distribution System reduces operational cost (up to 40%), installation time and space.